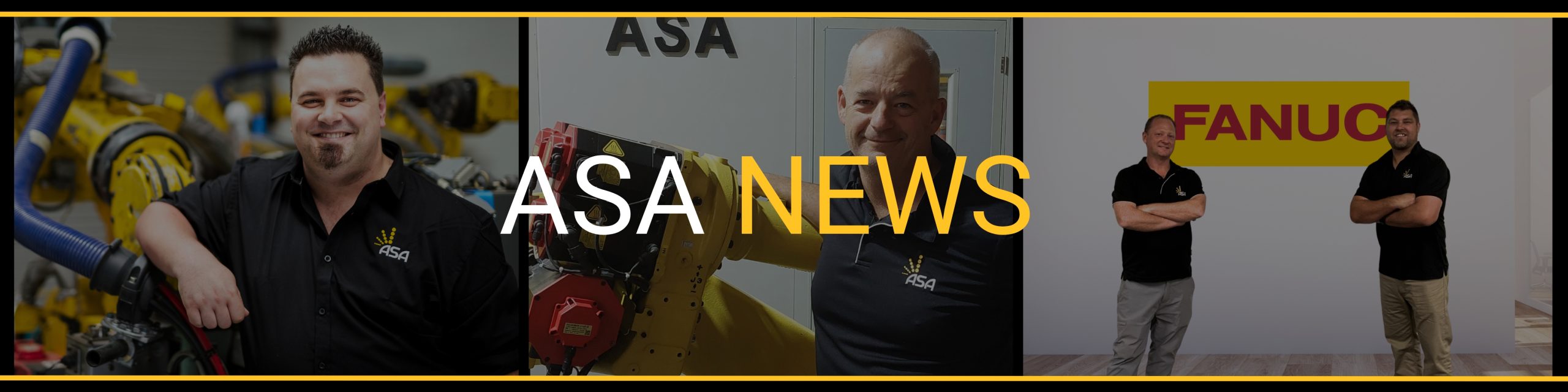
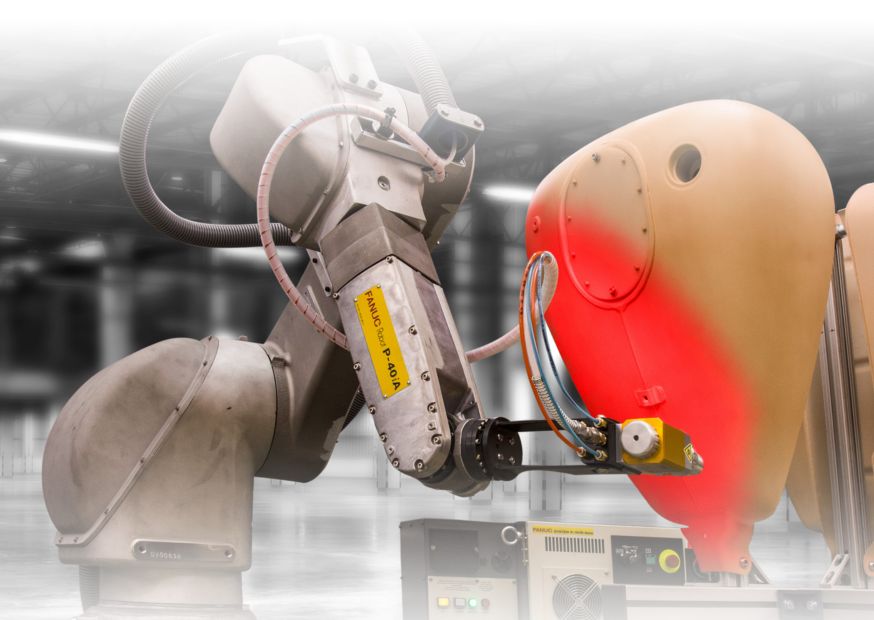
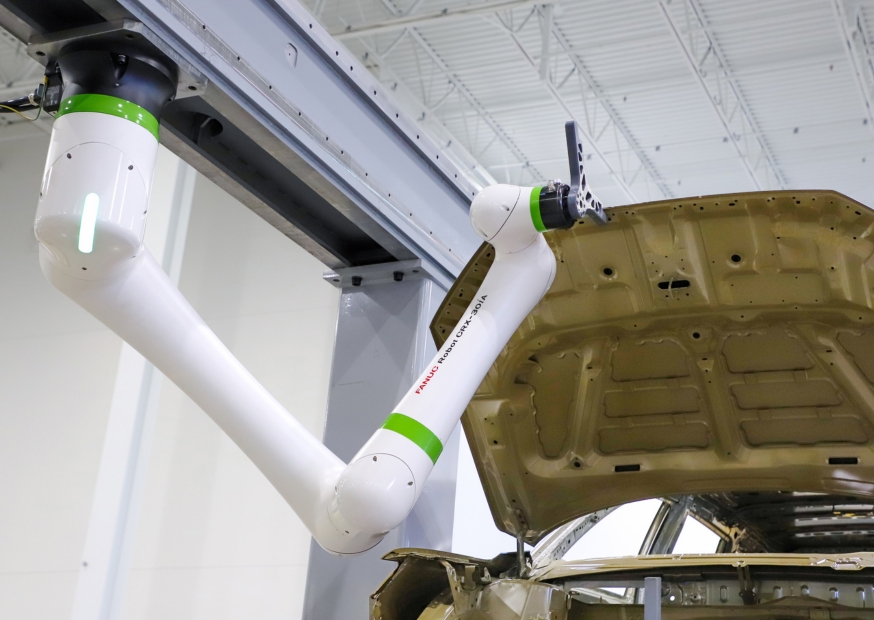
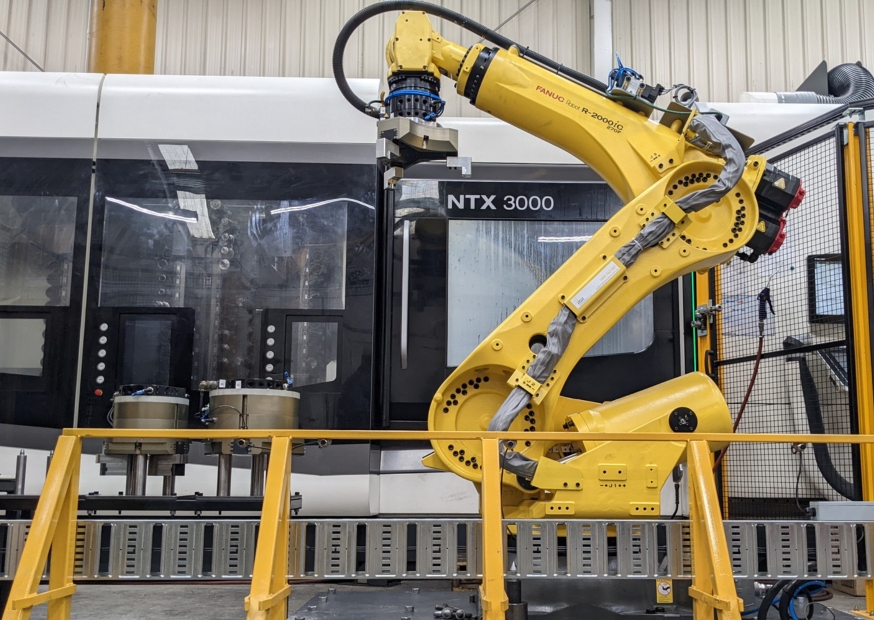
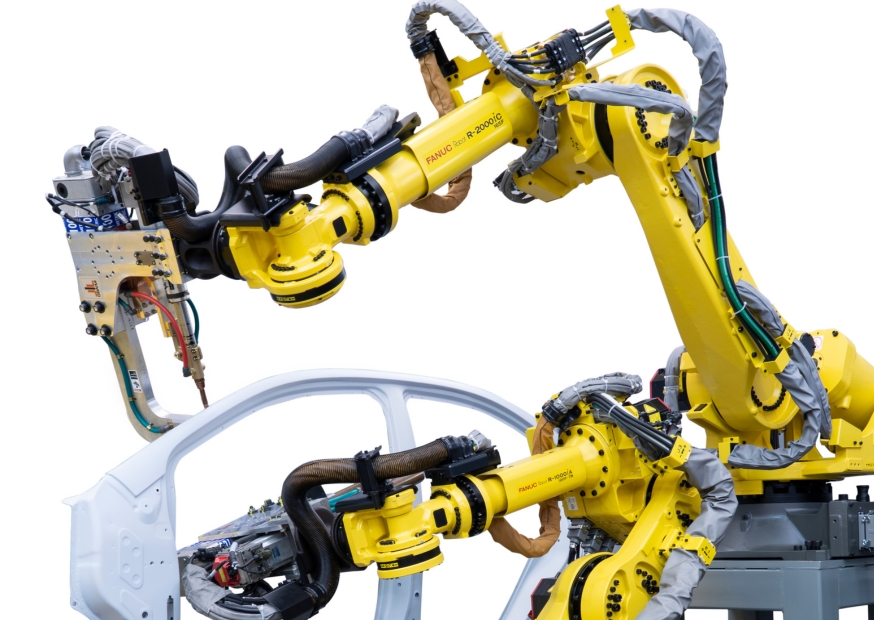
Industrial Robotics Companies: FANUC and ASA Leading the Way
In today’s fast-paced manufacturing world, industrial robotics companies drive transformation by boosting efficiency, improving productivity, and enhancing safety. Such companies provide cutting-edge robotics solutions that help businesses reduce costs, enhance output quality, and streamline operations. Among these leaders, FANUC stand out for their innovative technology and industry leadership.
What Makes Certain Industrial Robotics Companies Stand Out Above the Rest?
Industrial robotics companies design and deploy robots that automate manufacturing processes, from simple repetitive tasks to complex assembly lines. By integrating robotics into operations, businesses cut down on human error, increase production rates, and create safer work environments. Furthermore, FANUC specialise in creating both industrial robots and collaborative robots (cobots), which safely work alongside humans to improve flexibility and efficiency.
FANUC: A Leader in Industrial Robotics
FANUC, a global leader in industrial robotics, has driven innovations in automation for decades. Known for their precision, reliability, and versatility, FANUC robots serve industries such as automotive, electronics, healthcare, and manufacturing. As a result, FANUC’s robots are highly regarded for their high performance and consistency.
FANUC robots excel at handling various tasks with high efficiency. Whether performing large-scale assembly operations or material handling, FANUC robots ensure precision and minimise downtime. In addition, FANUC’s collaborative robots (cobots) enable human workers to work side by side with machines, increasing productivity while maintaining safety.
FANUC robots thrive in various applications, including:
- Assembly and Pick-and-Place Operations
- Welding and Painting
- Packaging and Material Handling
- Inspection and Quality Control
- Machine Tool Tending
This commitment to continuous innovation makes FANUC a trusted choice for industrial automation worldwide.
Automated Solutions Australia (ASA): Bringing Robotics to Local Markets
Automated Solutions Australia (ASA) plays a vital role in the robotics market, especially across Australian. As a leader in industrial automation, ASA partners integrates FANUC robotic systems to offer businesses state-of-the-art robotics solutions that drive operational efficiency. Consequently, ASA is able to help Australian companies take full advantage of the latest robotics technologies.
ASA provides tailored robotics integration services, ensuring businesses of all sizes can seamlessly incorporate industrial robots into their workflows. With this expertise, ASA spans a range of industries—manufacturing, mining, electronics, and more—and helps companies optimise their operations with FANUC robots and cobots.
By offering localised support and guidance, ASA ensures businesses maximise the potential of robotics technology. Whether automating specific workstations or transforming entire production lines, ASA provides the expertise necessary to meet each business’s unique needs.
Why Partner with Industrial Robotics Companies Like ASA?
Partnering with leading industrial robotics companies like ASA brings numerous benefits:
- Increased Productivity: Robots work tirelessly, driving production output without breaks, reducing downtime.
- Enhanced Quality Control: Robots consistently perform tasks with precision, ensuring high-quality, defect-free products.
- Improved Worker Safety: Robots take over dangerous and repetitive tasks, improving safety for human workers.
- Cost Efficiency: Although robots require an initial investment, businesses save on labor costs and productivity increases, delivering a fast return on investment.
- Scalability: ASA provides solutions that grow with your business, adapting to new challenges and expanding production needs.
Why Choose FANUC and ASA for Your Robotics Solutions?
By choosing FANUC robots through Automated Solutions Australia (ASA), businesses gain access to world-class automation solutions. In turn, FANUC’s advanced robots integrate seamlessly into a variety of industries, helping Australian businesses stay competitive in the global market.
FANUC robots bring industry-leading technology, and ASA ensures businesses can maximise their potential through expert integration and support.
Industrial robotics companies are changing the future of manufacturing and automation. Whether you’re looking to automate a specific task or overhaul your entire production process, we offer the cutting-edge robotics solutions necessary to improve efficiency, safety, and overall performance. Partner with ASA to unlock the potential of your operations and stay ahead in the competitive world of automation.
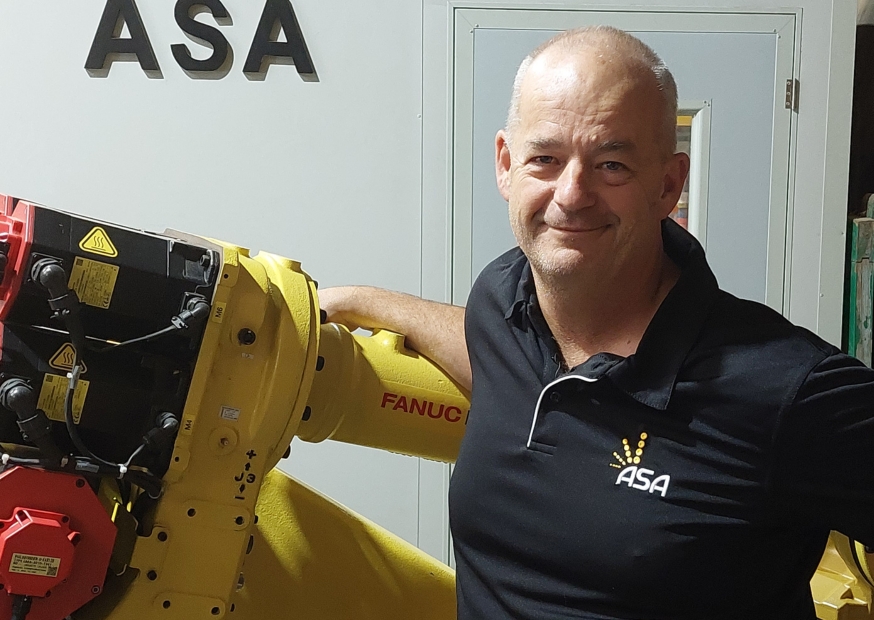
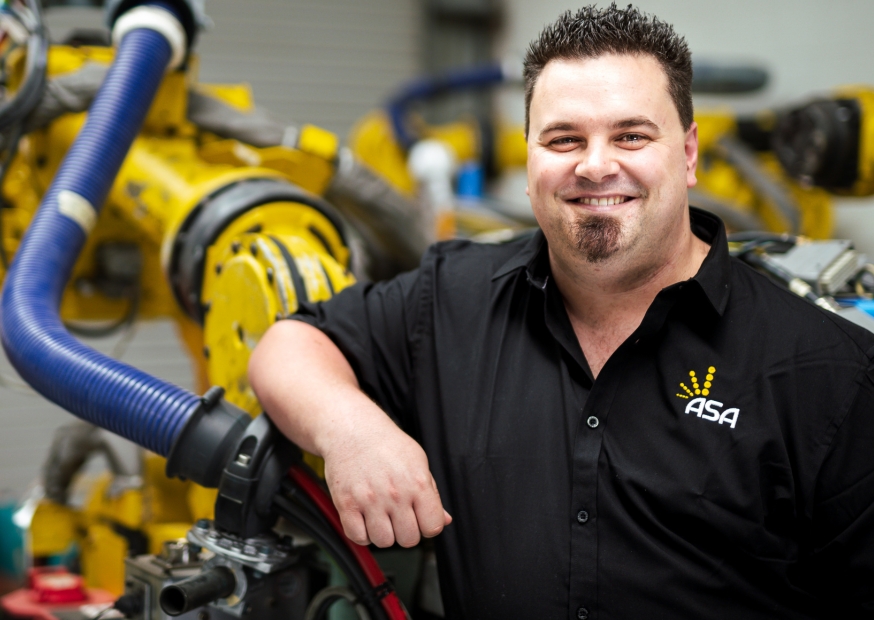
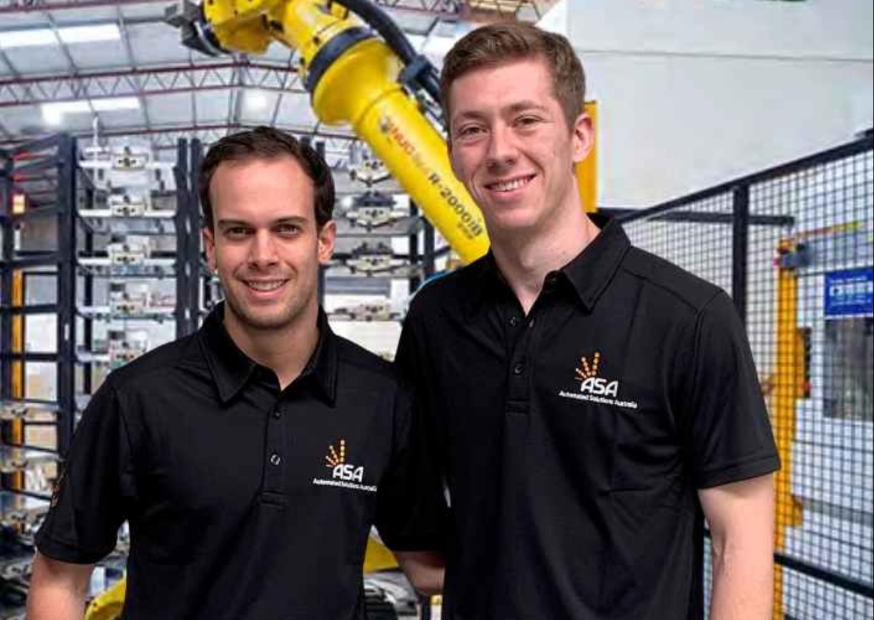
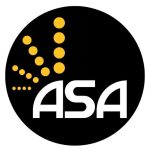
Send an enquiry
Click an Application to Explore Further:
FANUC Robots Australia | Paint Robots for Surface Finishing | Welding Robots by FANUC | Machine Tool Tending Robots | Fibreglass and Gelcoat Robots | Palletising Robots | Robotic Vision Inspection Systems | Plastics Painting | Deburring and Polishing | Sealing and Dispensing | Picking and Packaging | Material Removal Robots | Shot Blasting and Peening | Materials Handling Robots |
More (Recent) News Stories from Automation Solutions Australia:
Types of Welding Robots | Paint Mate | Australian Robotics | SCARA Robots | Robot Suppliers |Automation Robotics | Fibreglass Coating | Industrial Automation Industry | Manufacturing Automation | Welding Robot | Industrial Robotics Industry | Automatic Systems | Automated Manufacturing System | Auto Robots | Automatic Material Handling | Picking Robots | CNC Machinery Solutions | Australia Wide Automation | Automatic Coating | Collaborative Robots in Manufacturing | Automatic Solutions | Automated Robot | Robotics Integrators | Robotic Solutions | PLC Industrial Automation | Automated Materials Handling | Robots Used in Industry | Cobot Integration | Palletisers | Robotic Spot Welding | Industrial Robots for Sale | Robots in Business | Collaborative Welding Robots | Robot Solution | Adelaide Automation | Shot Blasting Services | Cobots and Robots |