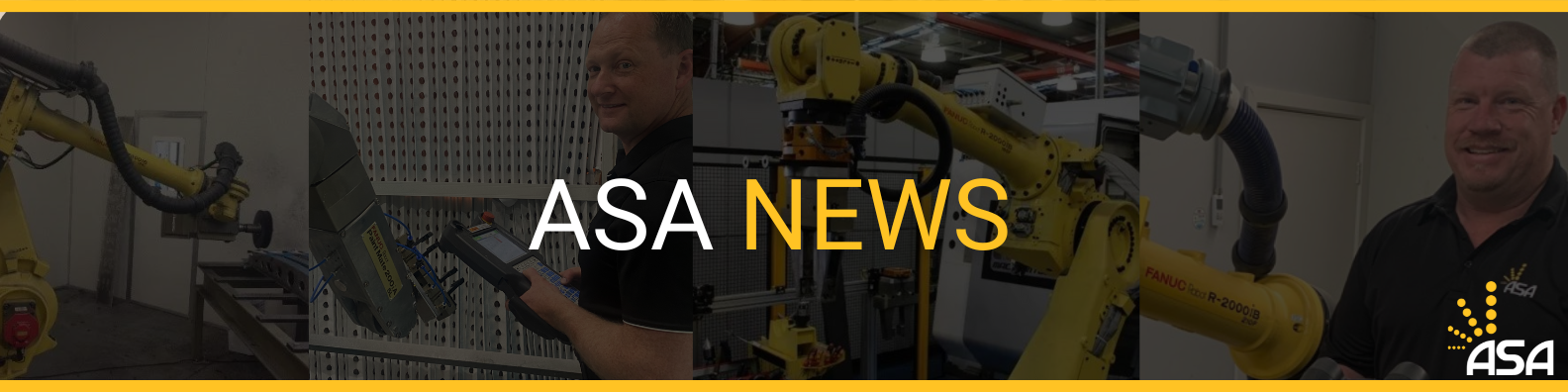
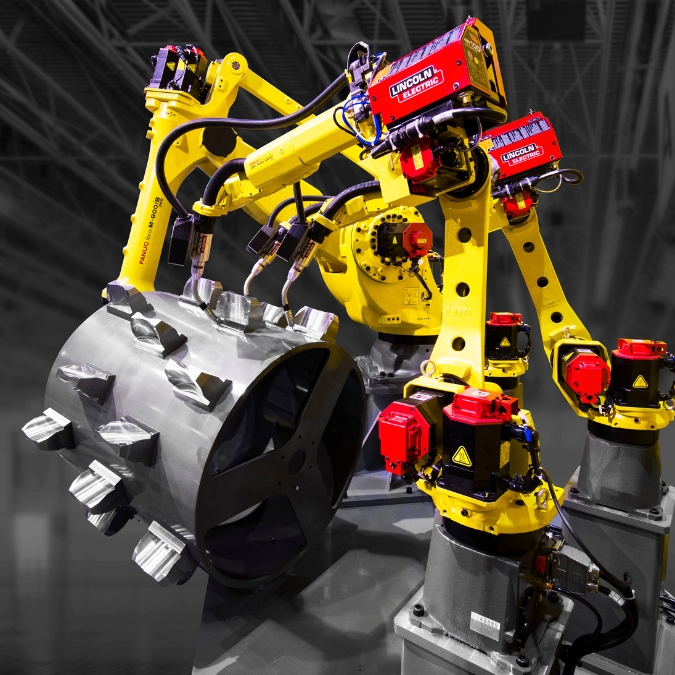
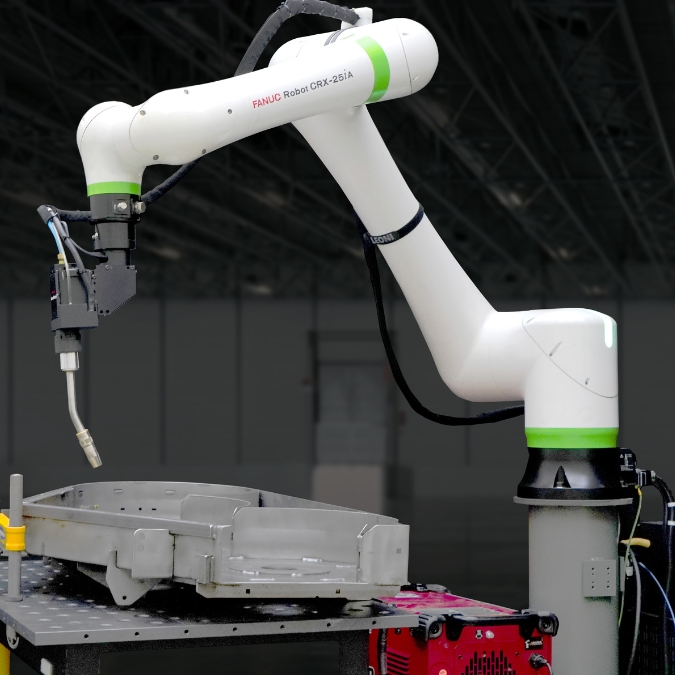
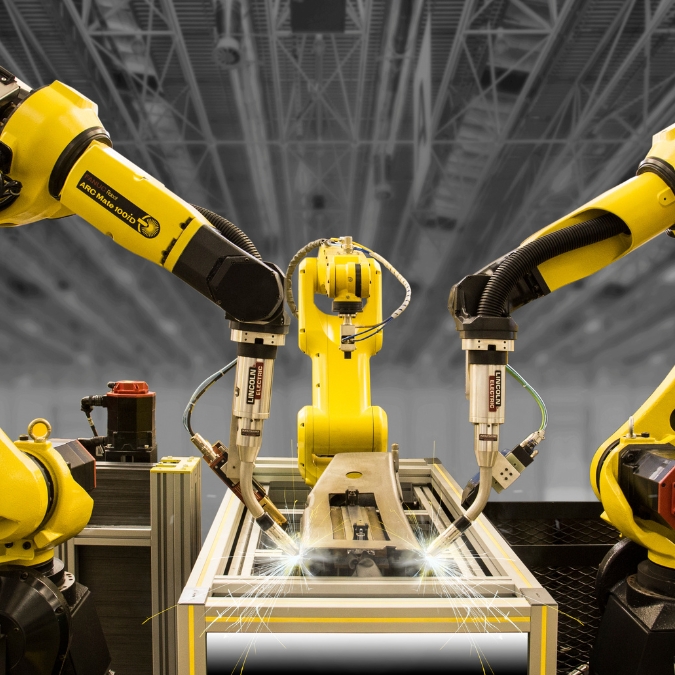
The Future of Automated Welding
In today’s rapidly evolving manufacturing landscape, the integration of advanced technologies is crucial for staying competitive. One such technology that is transforming industries is automated welding. Consequently, it is redefining traditional processes, offering unparalleled precision, efficiency, and productivity. In this article, we will delve into the details of automated welding, exploring its benefits and applications.
What is Automated Welding?
To begin with, automated welding refers to the use of robotic systems and advanced machinery to perform welding tasks. Therefore, they can carry out repetitive welding tasks with high precision and consistency. Such systems are typically equipped with sensors, controllers, and unlike manual welding, automated welding allows you to operate with minimal human intervention. Additional software can enable them to adapt to various requirements and conditions.
Benefits of Automated Welding
First and foremost, automated welding offers significant benefits over traditional methods. Here are some key advantages:
Increased Productivity: Such systems can work continuously without breaks, significantly boosting production rates and throughput. Consequently, manufacturers can meet higher demands and reduce lead times.
Enhanced Precision and Consistency: Robots perform welding tasks with high accuracy, ensuring uniform weld quality. This consistency is particularly important in industries where precision is critical, such as aerospace and automotive manufacturing.
Improved Safety: Welding involves hazardous conditions that can pose risks to human workers. Automated welding systems minimise human exposure to dangerous environments, thereby enhancing workplace safety.
Cost Savings: While the initial investment in automated welding systems can be high, the long-term savings are substantial. Reduced labor costs, fewer errors, and less rework contribute to significant cost savings over time.
Flexibility: You can program automated welding systems to handle a wide range of tasks and materials.This flexibility allows manufacturers to adapt to changing production needs and diversify their product offerings.
Applications of Automated Welding
Some common applications include:
Automotive Industry: The automotive industry widely uses systems for tasks such as body assembly, frame construction, and exhaust system fabrication. The precision and speed of automated welding ensure high-quality welds in vehicle manufacturing.
Aerospace Industry: In the aerospace sector, automated welding is crucial for constructing aircraft components, including fuselages and engine parts. The high precision and reliability of automated systems meet the stringent quality standards required in aerospace manufacturing.
Construction Industry: Automated welding is employed in the construction of steel structures, bridges, and pipelines. The efficiency and accuracy enhances the durability and safety of these structures.
Manufacturing Industry: It’s also prevalent in general manufacturing for fabricating machinery, equipment, and consumer goods. The ability to handle complex welds and high volumes makes automated welding indispensable in manufacturing.
Automated Welding with Automated Solutions Australia (ASA)
At Automated Solutions Australia (ASA), we integrate advanced automated welding systems to enhance manufacturing processes. With over 20 years of experience, ASA has established itself as a leader in the field, providing innovative solutions tailored to meet the unique needs of our clients. We exclusively integrate the FANUC range of welding robots, renowned for their reliability, precision, and advanced capabilities.
Why Choose ASA for Your Automated Welding Needs?
Expertise and Experience: Our team of skilled engineers and technicians has extensive experience in automated welding integration. We understand the complexities of various industries and deliver solutions that enhance productivity and efficiency.
Cutting-Edge Technology: We leverage the latest FANUC welding robots, which are designed to handle a wide range of welding tasks with unmatched precision. These robots come equipped with advanced features such as adaptive control and real-time monitoring.
Comprehensive Support: From initial consultation and design to installation, programming, and maintenance, ASA offers end-to-end support. Our commitment to customer satisfaction ensures seamless integration and optimal performance.
In conclusion, automated welding is transorming the manufacturing industry, offering numerous benefits in terms of productivity, precision, safety, and cost savings. For businesses looking to stay competitive and embrace the future of welding, ASA is your trusted partner. Contact us today to learn more about our automated welding solutions and how we can help you achieve your automation goals.
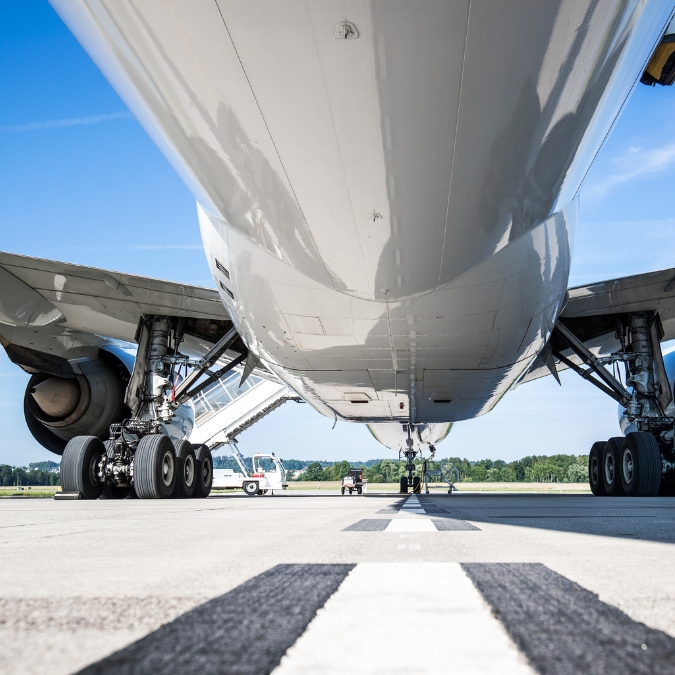
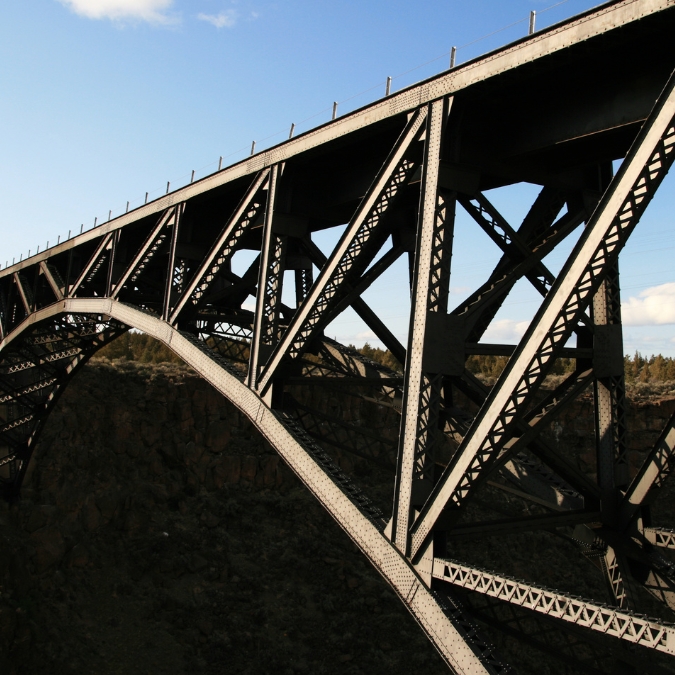
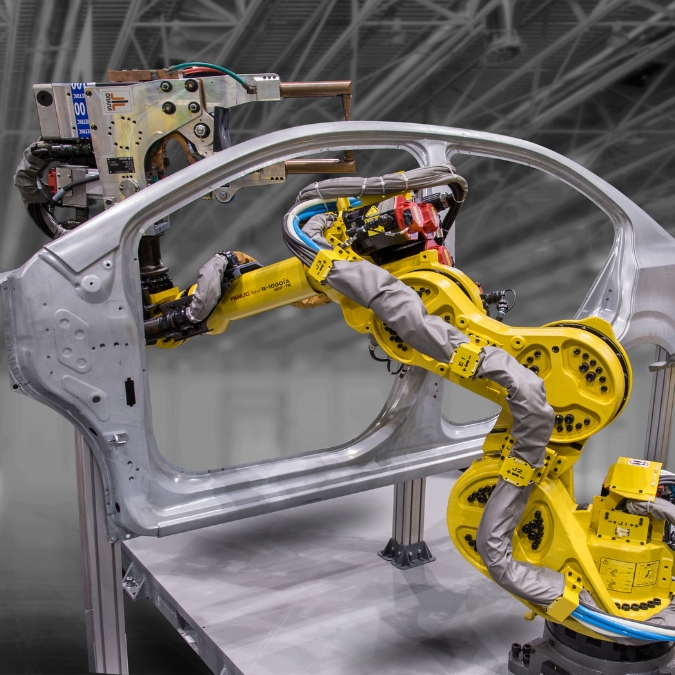
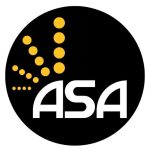
Send an enquiry:
Click an Application to Explore Further:
FANUC Robots Australia | Paint Robots for Surface Finishing | Welding Robots by FANUC | Machine Tool Tending Robots | Fibreglass and Gelcoat Robots | Palletising Robots | Robotic Vision Inspection Systems | Plastics Painting | Deburring and Polishing | Sealing and Dispensing | Picking and Packaging | Material Removal Robots | Shot Blasting and Peening |
More (Recent) News Stories from Automation Solutions Australia:
| Advantages of Robotic Welding | 6 Axis Welding Robots | FANUC Robot Programming | Paint Finishing in Australia | Industrial Manufacturing | Robot Integrator in Australia | Automation and Robotics | Industrial Applications of Robots | Robot Welding | Automation Engineering | Benefits of Robots | Materials Handling in Australia | Robotic Assembly Guide | A Guide to the History of Robots | Robotic Laser Welding | Robotics in Business | Laser Welding | Picking and Packaging | Grit Blasting Explained | Robotic Lathe and Milling | Robotic Integration | Programmable Logic Controllers | Robotic Mig Welding | Robotic Dispensing | Robotics and Automation Engineering | Automation Companies Aus | Robotics Companies | Robotics Industry Aus | Robots and Machines |