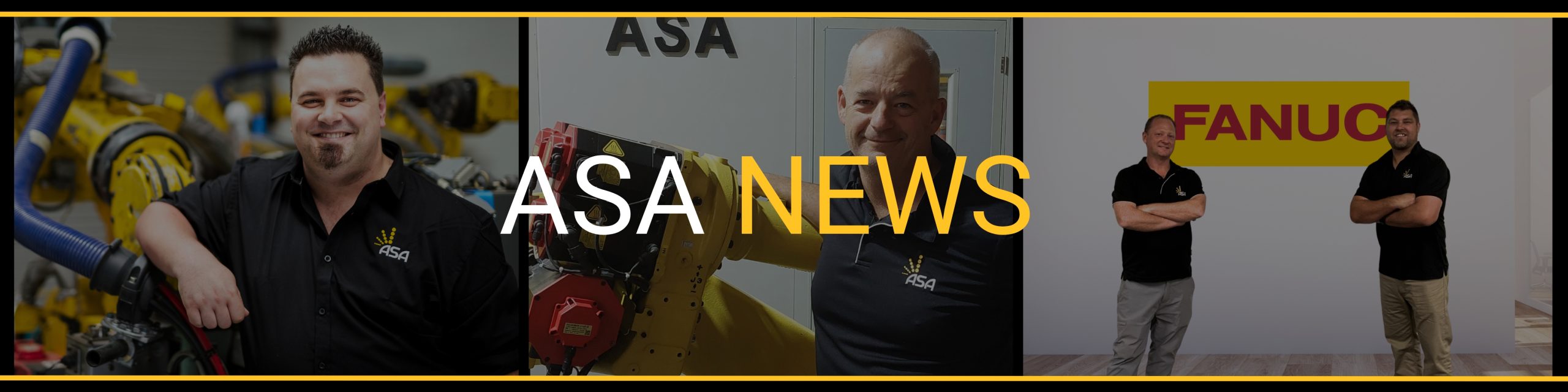
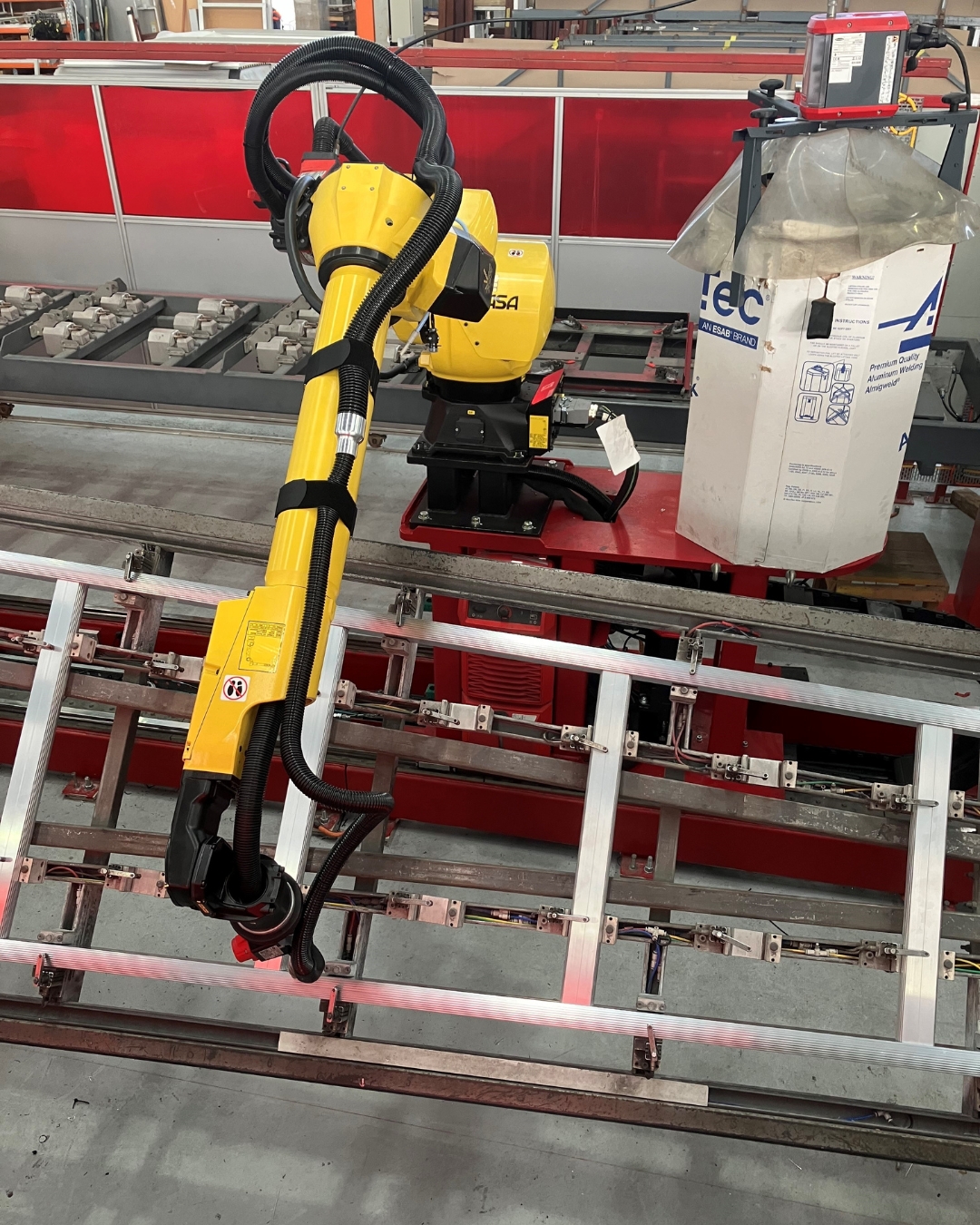
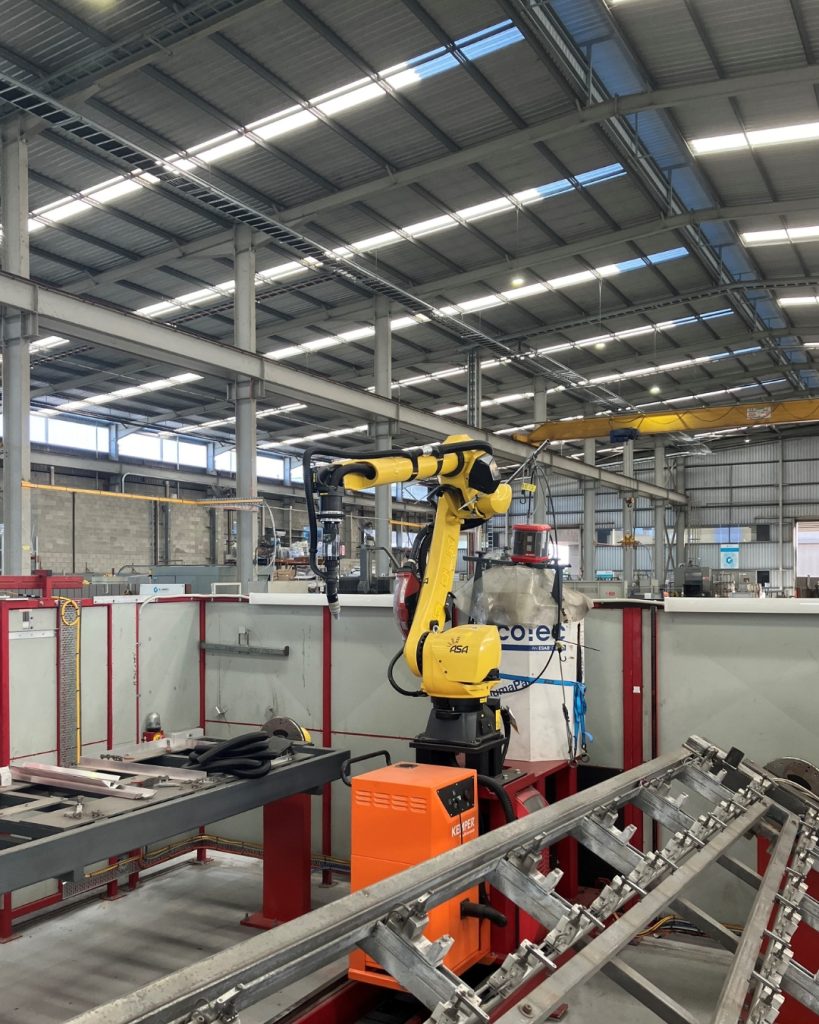
In a recent project that highlights the synergy between technology and industry, Automated Solutions Australia (ASA) collaborated with QuickAlly Access Solutions to upgrade their welding capabilities at their Brisbane facility. This project is a perfect example of how innovative automation solutions can enhance manufacturing processes, particularly for a company as committed to quality and safety as QuickAlly.
QuickAlly Access Solutions is a key player in the Australian market, known for their high quality scaffolding and access platforms. As part of the G.James Group of Companies (Est. 1917), QuickAlly has a long standing reputation for producing durable and reliable products that meet the highest safety standards.Their product range includes scaffolds, platforms, trestles & planks, stair treads and saw benches, all engineered to comply with Australian Standards.Additionally, QuickAlly specialises in creating customised work platforms for industries such as road, rail, aviation, marine, and industrial applications, further cementing their position as a leader in the field.
The collaboration between ASA and QuickAlly focused on replacing an aging REIS welding robot with a new, state of the art FANUC ArcMate 120iD/12L robot and 2x servo rotary positioners. This upgrade is a significant step forward in ensuring that QuickAlly remains at the forefront of manufacturing excellence. The new system, which also includes offline weld path programming software, offers enhanced efficiency, precision and flexibility in QuickAlly’s welding operations.
The FANUC ArcMate 120iD/12L robot was chosen for its proven track record in the welding industry. With its 2272 mm reach and 12kg payload capacity, the robot is designed to handle the rigors of industrial welding with ease. Its hollow wrist design minimises stress on cables, reducing maintenance needs and prolonging the system’s lifespan. A failure the Quick Ally Team had experienced many times.
The robot’s integration with an advanced rail axis drive and ASA-supplied FANUC servo positioners allows for precise, multi-axis coordinated motion, ensuring optimal welding performance across all fixtures.
The cell was relocated to a new factory and at the same time, a completely new control system was designed and built by ASA, ensuring compliance to latest industry safety standards as well as ensuring high equipment uptime. The field devices were assessed and repurposed if suitable or replaced with new hardware where required.
One of the standout features of this upgrade is the incorporation of automatic offline programming software. This offline programming tool enables QuickAlly to develop and refine welding programs without interrupting production, providing a significant boost in operational efficiency. The software’s ability to automatically identify welds from CAD models and generate robot code streamlines the entire welding process, from planning to execution.
Our highly collaborative approach with this unique customer allowed us to achieve impressive results in record time. QuickAlly not only tore down the existing welding cell but also relocated it to its new location. Then, working closely together, ASA and QuickAlly reassembled the system. This teamwork enabled the project to move from disassembly to the first welds in just 4 days onsite, with production welds completed in less than 7 working days. This efficient process ensured that QuickAlly could swiftly meet their production demands with a refreshed, highly capable welding system.
G.James spokesperson, Warren Reddicliffe reflects, ‘We have worked closely with ASA on a previous robotic installation, so expectations and the bar was already set high for a successful project and we were not disappointed with the end results. Welding of Aluminium presents many challenges and variables to achieve high quality results every time and we have found that already the quality and reliability of the FANUC supplied by ASA along with our Fronius TPS400 has surpassed expectations. The welding software introduced by ASA for programming allows us to make simple changes without downtime on the robot and ability to create programs more efficiently and ensures the welds can be replicated and repeated over the whole product, harder for us to achieve previously.’
This project underscores ASA’s dedication to providing tailored automation solutions that meet the specific needs of our clients. By partnering with QuickAlly, we’ve not only upgraded their welding capabilities but also contributed to their ongoing commitment to innovation and quality in Australian manufacturing. As automation continues to evolve, projects like this demonstrate the transformative potential of integrating advanced technology into traditional manufacturing processes.
To visit the website of QuickAlly, click here.
For Automated Solutions Australia’s home page, click here.
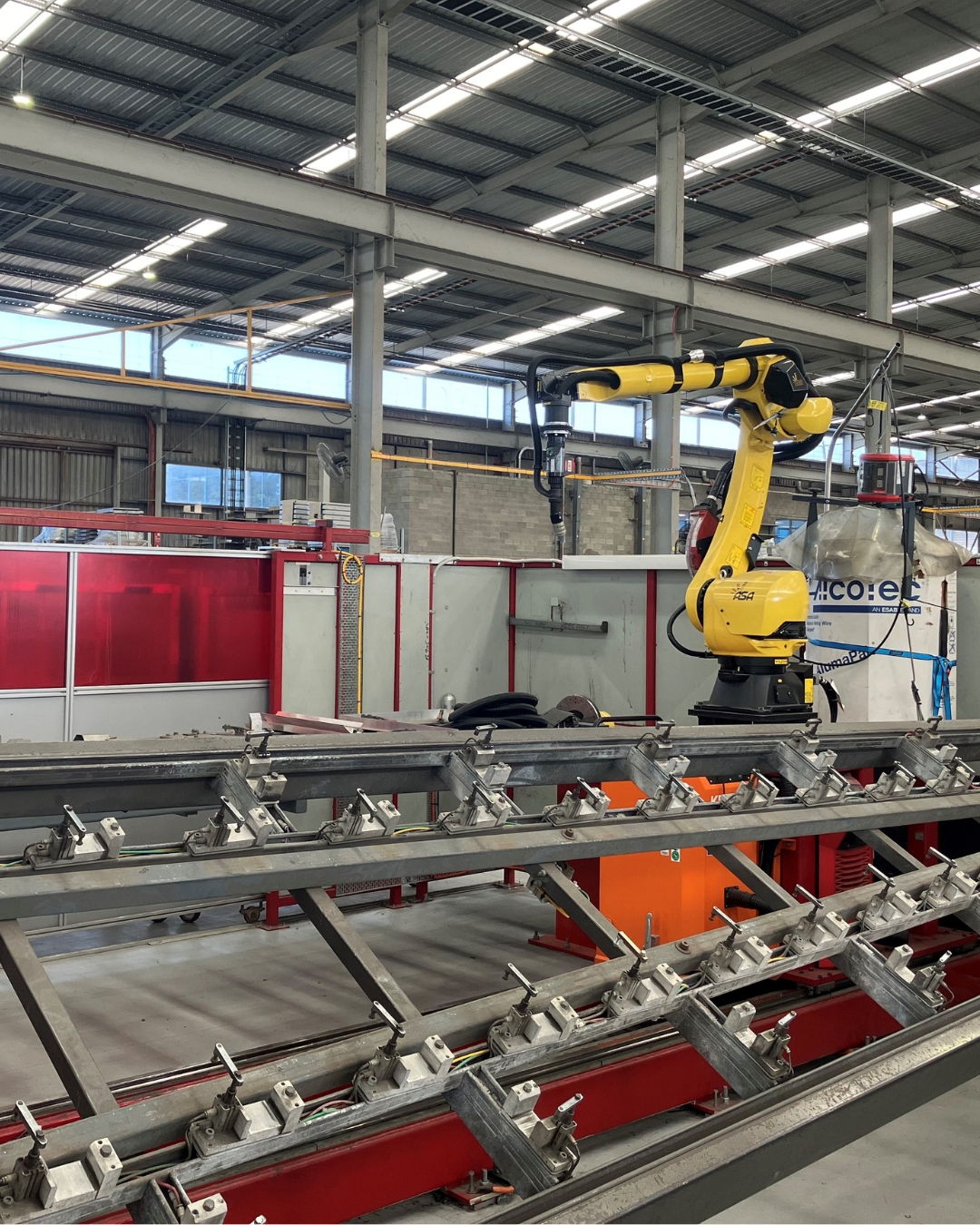
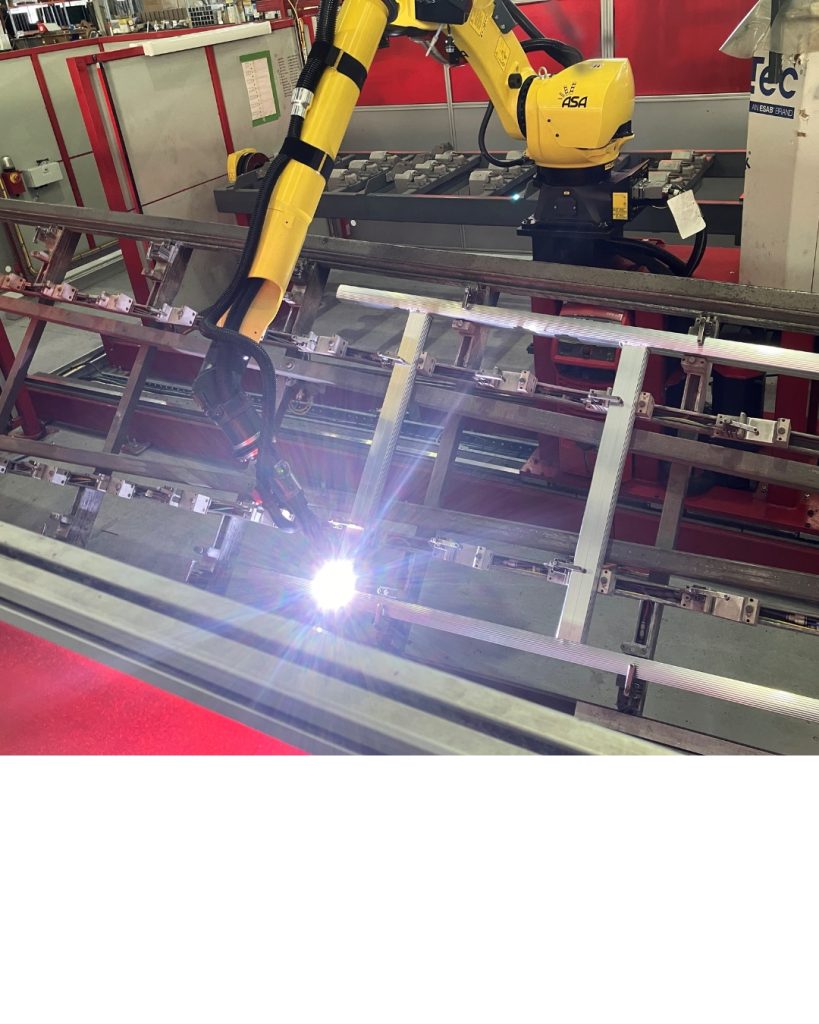
Send an enquiry:
Click an Application to Explore Further:
FANUC Robots Australia | Paint Robots for Surface Finishing | Welding Robots by FANUC | Machine Tool Tending Robots | Fibreglass and Gelcoat Robots | Palletising Robots | Robotic Vision Inspection Systems | Plastics Painting | Deburring and Polishing | Sealing and Dispensing | Picking and Packaging | Material Removal Robots | Shot Blasting and Peening |
More (Recent) News Stories from Automation Solutions Australia:
| Robot Welding Cell | Automated Picking Robots | Advantages of Robotic Welding | 6 Axis Welding Robots | FANUC Robot Programming | Paint Finishing in Australia | Industrial Manufacturing | Robot Integrator in Australia | Industrial Applications of Robots | Robot Welding | Automation Engineering | Benefits of Robots | Materials Hnadling in Australia | Robotic Assembly Guide | A Guide to the History of Robots | Robotic Laser Welding | Types of Welding Robots | Paint Mate | Australian Robotics | SCARA Robots | Robot Suppliers |